What is Stress Corrosion Cracking (SCC)?
Stress Corrosion Cracking (SCC) is a localized damage phenomenon that occurs in metal materials when exposed to specific corrosive environments while under tensile stress. In particular, ammonia storage tanks present conditions that are prone to SCC. For example, high tensile strength carbon steel is known to cause SCC in ammonia environments.
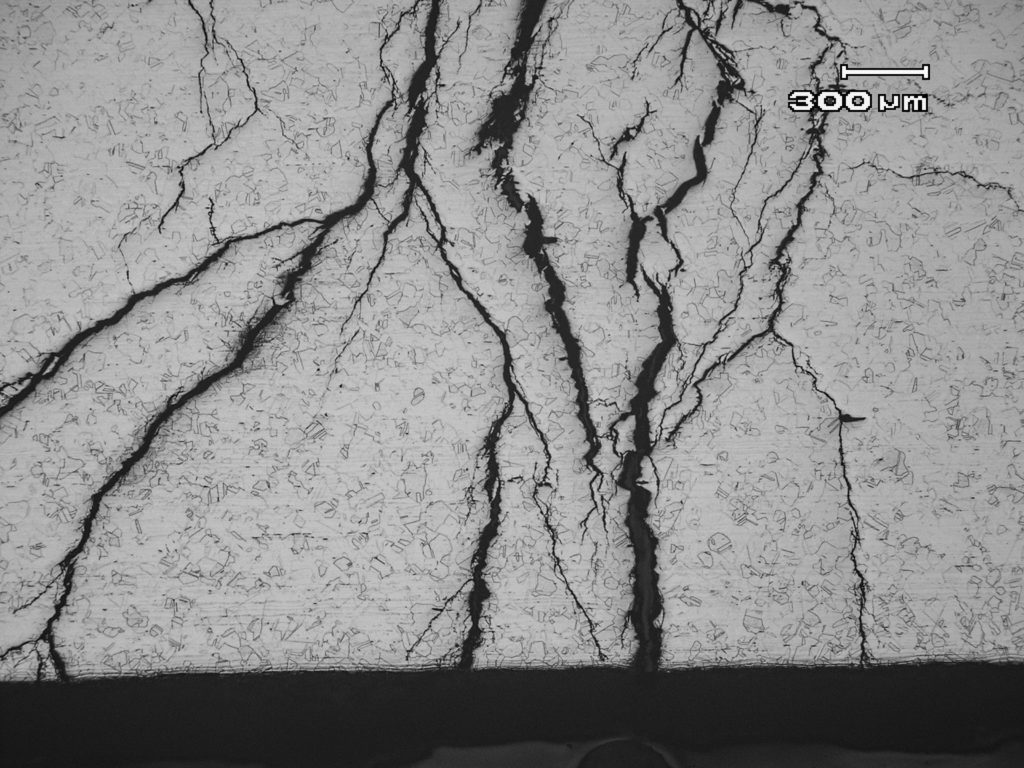
Our Solution: Shot Peening
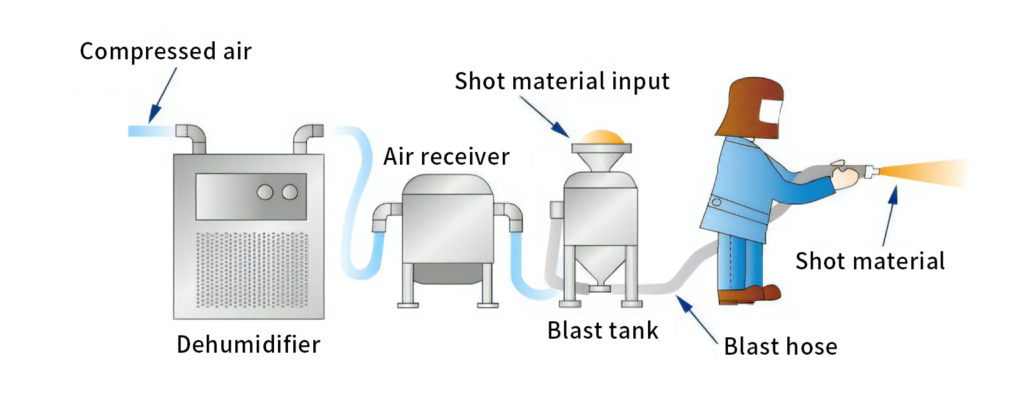
We recommend using "shot peening" as a countermeasure against SCC. Shot peening is a method that imparts compressive residual stress to the surface of metal by striking it with small spherical particles (shots) at high speed.
To avoid damage to the base material of the equipment, we select the optimal shot material according to the material and cost, and provide the highest quality implementation.
SCC Solution Comparison Chart
Technologies | Advantages | Disadvantages |
---|---|---|
Shot Peening | Remove tensile stress and apply compressive residual stress to eliminate the stress factor of SCC | If not managed with appropriate parameters, the effect may not be achieved at all. |
Material Switching | Improve corrosion resistance and mechanical properties (e.g., switching from SUS304 to Hastelloy C) | High cost, potential increase in SCC susceptibility in heat-affected zones such as welds |
Inhibitor Addition | Inhibit corrosion, and easily add to existing systems | Risk of contamination, difficult to manage inhibitor dosage, many SCC causative substances come from by-products, making identification difficult |
Thermal Spraying (Sacrificial Protection) | Electrochemically protect the base material (thermal spraying with zinc or aluminum) | The coating thickness gradually decreases, and during regular crack inspections, the coating must be removed, requiring periodic reapplication. |
Post Weld Heat Treatment (PWHT) | Reduce residual stress, and prevent weld embrittlement | Difficult to apply to large structures, cannot be applied to heat-affected zones caused by welding or grinding during construction, high-temperature treatment may cause buckling of the equipment |
We’ve been saving equipment from SCC across the globe.
We have successfully completed shot peening work on stainless steel spherical tanks for a petrochemical plant in Malaysia. They chose our premium shot peening service due to its semi-permanent and highly effective application, which is also suitable for stainless steel equipment. Additionally, we have numerous other successful projects in the Middle East and Southeast Asia, including Iran, Algeria, Singapore, and Indonesia.

Our Malaysia office is ready to help you!
Shot Peening Service Process
Step 1:Inquiry
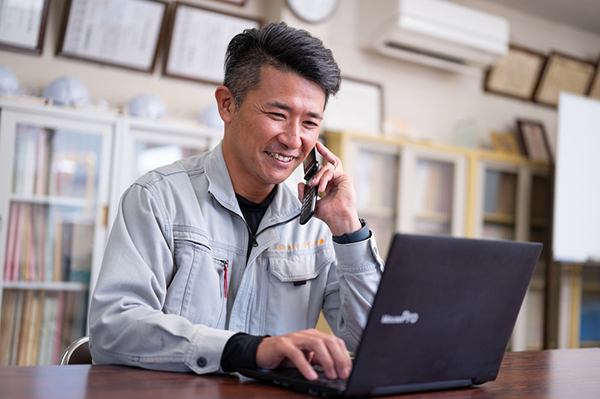
You can contact us through the inquiry form. At this stage, we conduct a detailed hearing of the customer's needs and issues.
Step 2: Consultation
& Assessment

We evaluate the current situation and gather information on-site to propose the optimal shot peening solution.
Step 3:Proposal
& Agreement
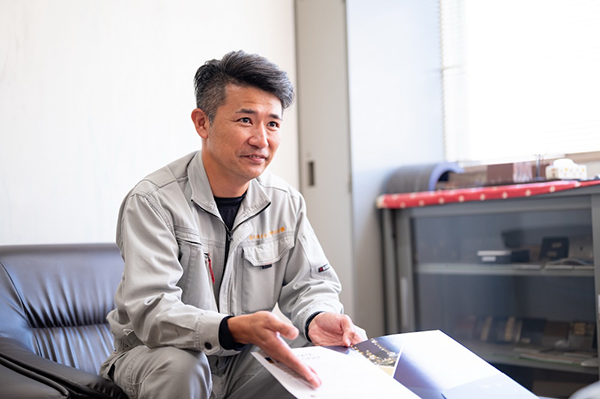
Based on the collected information, we make a tailored proposal. Once you agree with our proposal, we finalize the project details.
Step 4:In-Situ XRD
Measurement(optional)
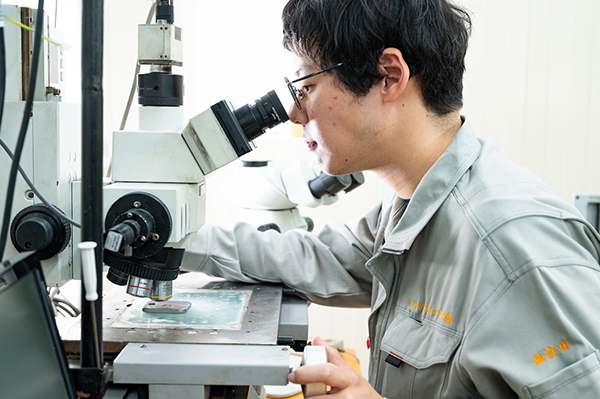
If necessary, we perform on-site X-ray diffraction (XRD) measurements to evaluates the current residual stress.
Step 5:Execution of
Shot Peening
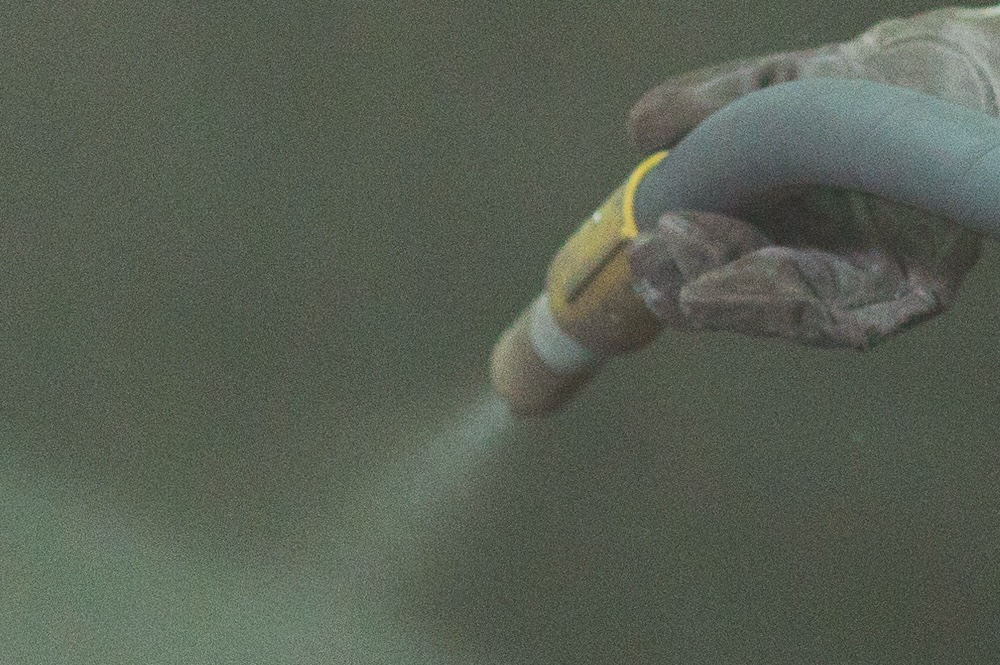
We execute shot peening with the selected shot material to avoid damage to the base material of the equipment.
Step 6: In-Situ XRD
Measurement(optional)
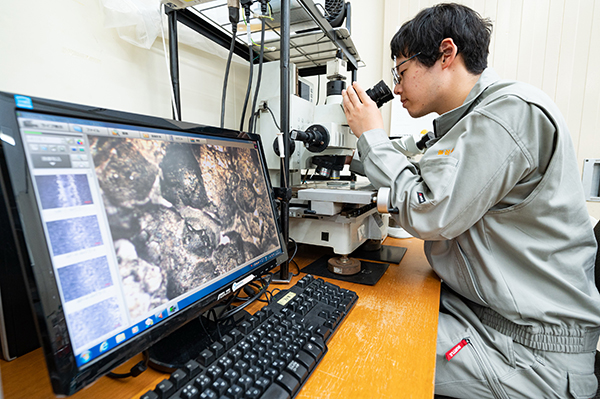
After shot peening, we perform XRD measurements again to check the residual stress post-treatment to verify the effectiveness.
Step 7:Inspection
& Reporting
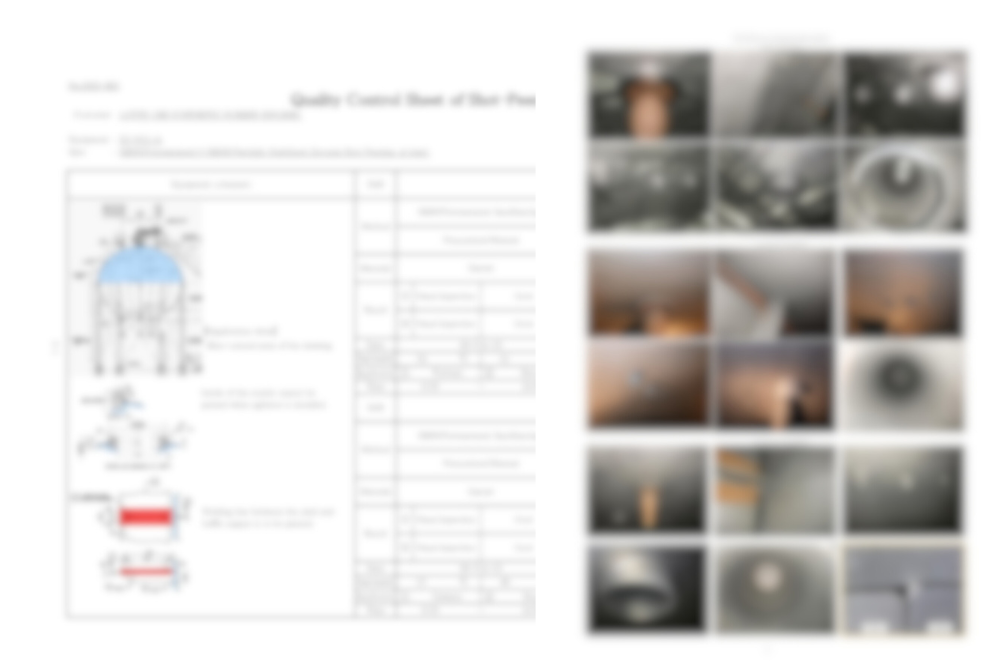
We conduct detailed inspections and reporting, providing feedback to the customer on the results and propose future maintenance.
Step 8:After Support
(if needed)
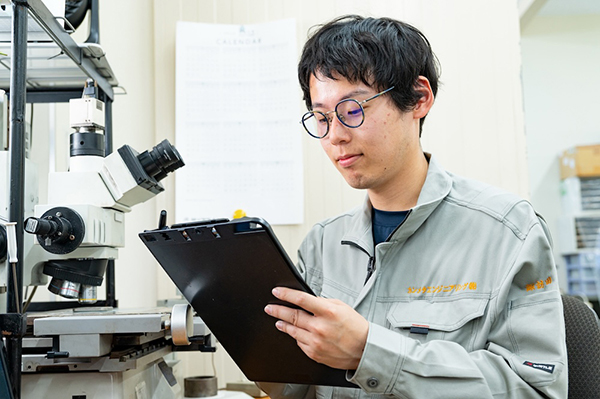
If necessary, we also support maintenance and additional treatments to sustain the effects of the shot peening.
Malaysia Office: KANMETA ENGINEERING (M) SDN. BHD.
Office location
Office No.4, MC-JTP Concept Sdn. Bhd, PLO 683, Jalan Keluli, Zon11, Pasir Gudang Industrial Area 81700, Pasir Gudang, Johor
Phone
Surface Treatment Specialists from Japan
Kanmeta Engineering Co., Ltd. is a specialist group in metal surface treatment technology, addressing corrosion, thinning, cracking countermeasures, and functionality enhancement for industrial equipment. Since its founding in 1953, we have utilized five proprietary technologies—anticorrosion thermal spraying, premium shot peening, premium fine peening, plasma coating, and cold spraying—to meet diverse industrial needs. We also provide high-quality on-site services both domestically and internationally.
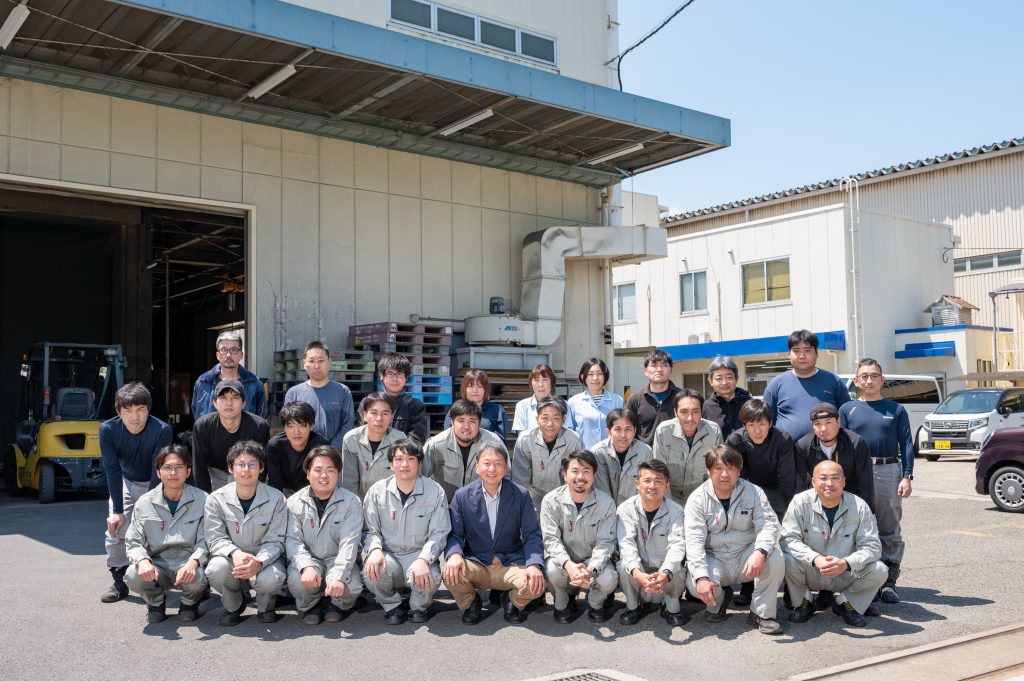
Inquiry
FAQs
Q1: What are the effects of shot peening?
Shot peening imparts compressive residual stress to the surface of metal by colliding countless small spherical particles (shot material) at high speed onto the metal surface. This compressive residual stress suppresses tensile stress, thereby preventing stress corrosion cracking (SCC) and fatigue failure. Additionally, it is expected to increase the hardness of the metal surface and improve wear resistance.
Q2: What types of parts and equipment can shot peening be applied to?
Shot peening can be applied to various metal parts and equipment. It is particularly used for structural components of aircraft and automobiles, pressure vessels, tanks, pipelines, gears, springs, and bearings. Since these parts are at high risk of fatigue failure and SCC, improving their reliability through shot peening is important.
Q3: How long does the effect of shot peening last?
The compressive residual stress imparted by shot peening lasts semi-permanently unless exposed to high-temperature environments or surface thinning due to severe corrosion occurs. However, in equipment such as agitator shafts and impeller welds that are subjected to resonant vibrations over long periods, stress reduction may occasionally occur. In such cases, it may be necessary to repeat the peening process every few years to a decade.
Q4: How long does it take to perform shot peening?
The time required for shot peening varies depending on the size, shape, and treatment area of the parts and equipment. Generally, it takes a few minutes to a few hours for small parts, and several days and weeks for large tanks or pipelines. Specific treatment times can be detailed during a preliminary consultation.
Q5: Is maintenance required after shot peening?
Post-shot peening maintenance generally does not require special care. However, for parts that are used for extended periods or in environments with high vibration or wear, regular inspections and re-treatment as necessary are recommended. This helps to maintain the effects of the compressive residual stress.